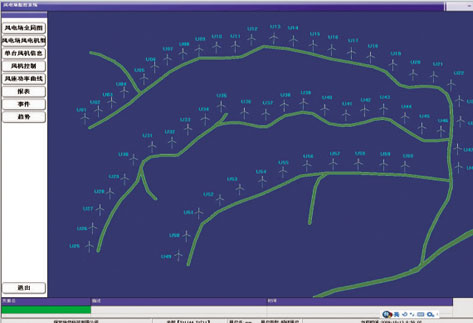
This system builds a full range simulator with the single wind power unit as the core and the whole wind power plant as the simulating object.
Single wind power unit simulation includes wind turbine, transmission gear, generator, rectifier and inverter device and the system of control and protection. As the wind power unit depends on the wind as its power source, the wind speed directly determines its dynamic characteristics. In this simulation system, the wind’s characteristics of randomness and intermittency are accurately described, using four elements to simulate: basic wind, gust and gradient wind and stochastic wind. At the same time, through the simulation of the wind power unit’s control systems and equipment such as the change of wind turbine blades, yaw, electric control, brake and protection, etc., its characteristics of operation and regulation are therefore accurately simulated, so as to the wind power plant’s normal operation and the dynamic response to a process of fault phenomenon and corresponding solution can be realistically simulated.
The power system simulation for the wind power plant includes hundreds of thousands of wind turbine units, each parallel connected with a capacitor and a transformer at its exit. Through the floor grid, each wind turbine is accessed to the nearby step-up substation and finally incorporated into the system. The power system simulation will be the simulation of its wiring mode and switch, bus, overhead line, cable, protection and automation device, etc.
The operation of wind power unit can be divided into four stages according to the difference of the wind speed.
▲The first operation area is the start-up phase when the wind speed rises from zero to cut-in wind speed. Under cut-in wind speed, the turbine is not tied to the power grid and it can't generate power. It cannot be tied to the grid until the wind speed is greater than or equal to the cut-in wind speed. The main task of this area is to achieve the synchronization control of the turbine. And the wind turbine control subsystem's mission is to adjust the rotating speed of the unit by changing the blade pitch with the variable pitch system, making it constant or change within a permitted range; The turbine control subsystem’s mission is to adjust the turbine’s stator voltage, ensuring it meet the synchronization condition, and practice the synchronization at the appropriate time.
▲The second phase is the constant rotating speed stage when the wind speed ranges from the cut-in speed to the maximum wind speed. At this stage, the turbine’s rotating speed always stays at the lowest speed, and the wind energy conversion coefficient gradually rises and reaches the maximum.
▲The third stage is the one from the wind speed corresponding to the maximum wind power coefficient to the rated wind speed. At this stage, the turbine speed rises from the lowest speed to the allowed highest speed. However, as the turbine’s rotating speed is restricted by the limit of the wind power unit’s electrical part, this stage is further divided into two operation areas, namely the variable-speed operation area (constant area) and the constant-speed operation area. In the variable speed area, the wind turbine’s power output will increase according to the increasing of the wind speed, and so does the turbine’s rotating speed, until to the allowed maximum speed (rated speed). In this area, the electrical control part of the doubly-fed induction turbine can control its rotating speed in order to track the change of the wind speed and maintain the best conversion coefficient.
In the constant speed area, the turbine’s rotating speed will keep the allowed maximum speed. The wind turbine output power will increase with the increase of the wind speed until to the maximum output power (rated power), at which point, the maximum output power’s corresponding wind speed is the rated wind speed.
▲The fourth stage is the constant power running stage when the wind speed ranges from above rated speed to cut-out speed. With the increasing of wind speed and power, power turbine and converter will reach its limit, so we must control its power at a level less than its power limit. When the wind speed increases, the unit’s rotating speed is reduced and the value decreases quickly so as to remain the power constant. The power control within the range of constant power is practiced by the wind turbine power control subsystem’s variable pitch control.
Simulation of wind power plant also includes centralized monitoring system. The central control room of remote monitoring can monitor the wind power unit’s state, electric parameters, temperature, wind speed parameters, etc.; Realize the function of the remote control of the wind power unit including remote start-up and shut-down, reset, etc; Realize the formation of online wind speed - power curve and various statistical reports, etc.
Wind power unit simulator can be used to train the operators of wind power plant and the students at school, improve the level of operation and control of the wind power unit and cultivate wind power technology talents. With the help of this system we can also further study the operation and control characteristics of wind power unit, validate and optimize the system design and contribute a lot in the development of wind power industry in our country.